Understanding the Importance of API Testing and Why You Should Be Doing It
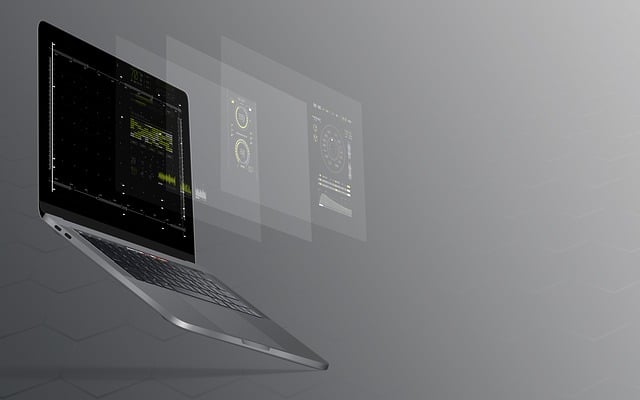
So what is API testing exactly and why is it important part of your app development process? First of all, let’s first define what API (Application Programming Interface) is. Put simply, an API is a set of functions, procedures, and other points of access which applications or operating systems make available to programmers that allows it to interact with other software. It’s somewhat similar to a user interface, but acts as a direct software connection to lower-level functions and operations. APIs are more complex in that usually only trained, knowledgeable programmers deal with them. With that out of the way, the next question is: what’s API testing? API testing focuses on the business logic layer of the application, which works on a much deeper level than other types of testing. This is different from GUI testing, which is able to test the look and feel of an application. Instead of using user inputs and outputs, you use software to send calls to the API. You then receive an output and note down the system’s response. Depending on the testing environment, you’ll most likely be writing your own code to test the API. Programmers should consider using an API testing tool…