Anyone involved in the field of welding knows that it’s not a skill fit for just anyone. It takes extensive training and years of experience to be at the top of the profession and to be successful in the most demanding welding situations. If you want to learn to weld, you can find New Jersey welding schools here.
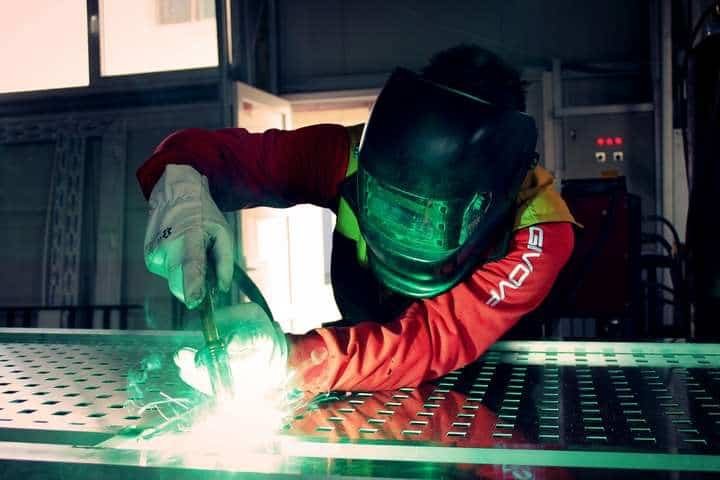
The only way for a skilled welder to be successful is to have the right tools. This includes more than just the actual welding apparatus and incorporates safety gear and traditional hand tools. Let’s look at how each of these areas can play a role in the successful work of a welder.
The Welder Itself
The days of bonding pieces of iron together are gone, with most of that work relegated to the shade tree mechanic. Today’s industrial applications involve countless specialized alloys, and joining them durably and effectively requires precision equipment built for that specific job.
Using equipment like friction stir welding tools and applications is ideal for these demanding situations. Their equipment can handle the full range of metals, from cool-welding aluminum through steel and nickel alloys that require the highest temperatures. Because the products built in these processes are used in high-pressure and life-safety applications, there is no room for compromise.
Hand Tools
Coarse welding for improvised purposes has a lot of room for error. If things aren’t held precisely in place, it’s no big deal; it’s not a CAD-built project anyway.
That’s not the case in today’s industrial welding. The specialized materials we already discussed are costly and cannot be wasted with mistakes. The designs are precise down to incredible increments, meaning there is no tolerance for imperfect sizing. The fine spot welds used in specialized arts and electronics demand perfect placement.
The clamps, mallets, and other hand tools involved in positioning materials must position things into a precise position and hold them there until the weld is complete. Any slippage can create a dangerous product or at the minimum, lead to unnecessary waste material.
Protective Gear
It can be easy to lose sight of just how dangerous welding is. It involves high voltage, high temperatures, and incredibly bright light that can destroy eyesight almost instantly. Skilled people who are building products must be thoroughly protected.
Masks usually come to mind first, and they’re certainly vital. Instant transitions in eye protection can protect users without forcing them to constantly raise and lower the face shield, allowing both hands to stay on the work and eliminating the risk of complacency. Gloves must not only deflect heat but must also resist cuts from sharp edges that can compromise their thermal protection, and details such as hoods, aprons, and sleeves cannot be overlooked when extremely high temperatures are involved.
Best Metals For Welding
Welding involves a highly complex process. It combines metallurgy, heat, oxidation, the various states of matter, and electricity. Many complications can arise during welding such as weld failure. A welder can reduce weld failure and other welding-related safety risks by choosing an easily weldable metal without requiring many additional pre- or post-weld operations.
The best metal stocks that a welder or welding shop should keep for future projects include the following:
Low Carbon Mild Steel
This is one of the metals with excellent weldability because of its abundant availability and demand. Low carbon mild steel is more ductile than others due to its trace alloy elements and low carbon levels, preventing microstructures and weld failures.
Aluminum
This metal is most sought for its corrosion resistance. Welders can weld aluminum without much difficulty, using the right techniques.
Stainless Steel
This metal is corrosion-resistant and weldable even if it has a complex chemical composition. Stainless steel types include ferritic, martensitic, and austenitic. Ferritic stainless steels and austenitic stainless steels are weldable.
Other Metals
The other metals suitable for welding include titanium, high carbon steels, and some superalloys. These metals usually require special shielding or treatment preparations.
Welders can buy aluminum stock, stainless steel, and low carbon mild steel online or at offline welding supplies stores.
Final Word
Welding is a fundamental vocation. The work of skilled welders has resulted in everything from skyscrapers to aircraft carriers and even electronics. But the quality of their work is only as good as combining their skills and their use of high-quality tools and equipment for building the final product. With a good setup in the factory or shop, right down to what the welder wears, the work coming out will be well-made, safe, durable, and even beautiful.