Modern electronics demand more and more advanced PCBs. They need to be denser, more reliable, and more complex. Traditional PCBs cannot always provide expected characteristics, so PCB manufacturers are investing in advanced PCB manufacturing equipment to make advanced PCBs at a rapid pace and low cost.
Common types of advanced PCBs
Generally speaking, an advanced PCB is a board that is manufactured differently than a conventional FR4 PCB. The different technological processes and materials define the advancement. Common types of advances PCBs are:
- Rogers
- HDI (Buried/blind vias)
- Aluminum
- Copper
- Flex
- Rigid-Flex
The list may not be complete as technology evolves, and there may be new technologies and materials be involved.
Each of the PCB technologies has its own purpose and place. Why you should use a different PCB than FR4 conventional PCB?
Rogers PCBs
Rogers PCB is the closest compared to FR-4. FR-4 base is made of woven fiberglass and epoxy resin binder with copper sheet laminate. It is a cheap and reliable material for most of its purposes. This is why it is so widely used. However, when it comes to high-frequency electronics, FR-4 starts failing due to losses in the material. This is where Rogers comes in. Instead of epoxy resin, it uses materials with better high-frequency properties, such as Teflon (PTEE). It is more expensive than resin, so Rogers is mainly used in RF circuits when necessary. Read on PCBGogo great material on Rogers vs. FR-4.
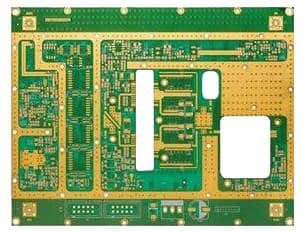
How to visually distinguish Rogers from FR-4. Rogers usually comes with lots of via stitching, shielding areas. Boards visually appear that are RF-related.
HDI PCB boards
HDI boards are widespread boards due to their ability to achieve high circuit density. This is achieved by pacing blind and buried vias between layers. Cell phones, wearable devices, and small PCB boards usually use HDI boards to achieve high small component density. Smaller component sizes, shorter signal path distances allow faster signal transmissions and less loss.
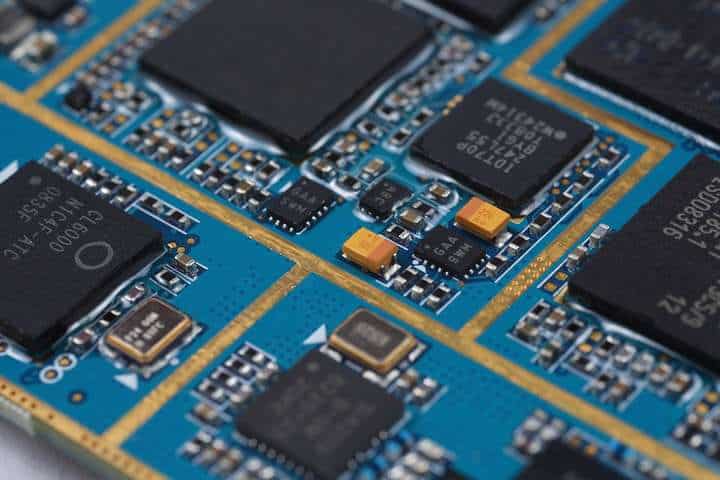
HDI technology is a small multilayer PCB and an optimized PCB where you may need fewer layers than conventional multilayer PCB. For instance, conventional PCB would require 8 layers to achieve the result, while HDI could fit into 4 layers. HDI boards are usually using micro-via technology where drilling is performed with the lasers reaching 1Mil accuracy.
Aluminum PCBs
Aluminum PCBs have their specific niche – LED lamps. This is a cheap material that is efficient in heat dissipation. Aluminum PCBs can be manufactured differently – with an aluminum core in the middle and on the bottom. Practically, aluminum substitutes fiberglass of conventional PCB. Of course, it is surrounded by dielectric so that traces could be routed.
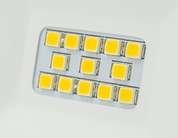
Aluminum PCB substrate:
- It is great for mechanical and thermal stability
- It is cheap as it is the common earth element
- Good heat dissipator – quickly cools localized high-power components such as LEDs
- Lightweight and durable
- It is easy to recycle and non-toxic
Aluminum PCBs are usually used in power LED applications, compact power supplies, power electronics such as solid-state relays.
Copper PCBs
Copper PCB properties can be compared to aluminum with one difference – copper has better thermal conductivity. However, this comes with a higher cost, as copper is more expensive than aluminum.
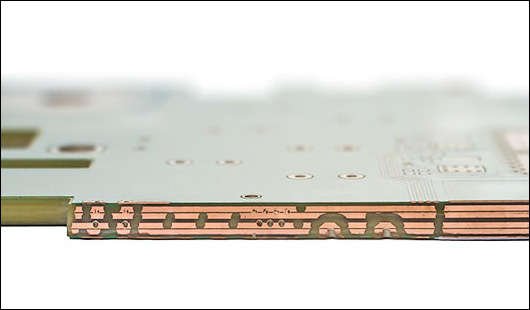
Copper PCBs are used in critical areas where thermal management is crucial. You can find copper PCBs in high-frequency power circuits. Also, copper is a bit easier to process than aluminum due to its different chemical and mechanical properties.
Flex PCBs
Flexible PCBs are wide topic as it is a different technology compared to conventional hard flat boards. Flexible PCBs allow designing free-form devices without geometrical restrictions. Take any camera; under enclosure, you will see that it is completely wrapped in flexible PCB. Such freedom gives the ability to design comfortable, small, and yet feature-rich devices.
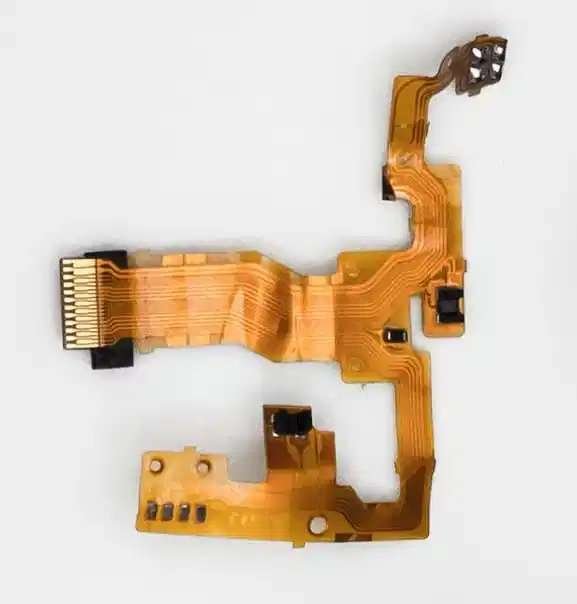
Flexible PCBs are similar to conventional PCBs with copper traces, but the base material is a polymer substrate. Traces may also be printed on the thick polymer film. The mechanical strength depends on substrate material and additives that may increase reinforcement. There can be multiple layers in flexible PCB, so no problem to make it very complex.
Let’s go through several advantages of flex PCBs:
- Design freedom – you are not restricted to geometrical constraints
- Organic look – flex PCBs look more natural and pleasing
- Potential cost reduction – with flexible PCBs overall electronics of the device can be cheaper
- Resistant to stress – better resistivity to vibrations and thermal stresses
- Takes less space – bending and shaping allows occupying less space on the device
- Less required components – no need to interconnect multiple boards
However, there are few limitations of flex PCBs:
- Circuits are less resistant to static electricity that can damage electronics
- Risk to tear and overbend – repair is difficult
- Les resistive to environmental factors – humidity, chemical fumes can damage circuits.
Despite the limitations, flexible PCBs are widely used in many devices to design sophisticated devices without shape restrictions.
Rigid-Flex PCBs
As the name says, rigid-flex PCBs bring advantages of both sides. Rigid part of PCBs delivers more density and better thermal properties, while flexible part allows easy interconnection between the boards without additional components and wires. Manufacturing of such boards is more complex, but avoiding many interconnecting elements overall cost may be even reduced.
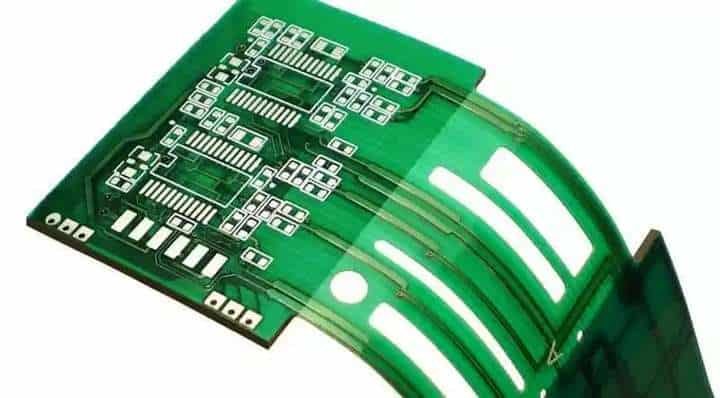
For instance, PCBgogo can manufacture up to 8-layers of rigid-flex PCBs of different thicknesses from 0.4 to 3.2mm. You can check out capabilities and calculate the approximate manufacturing prices using an online quote form.
Takeaway
Advanced PCBs are accessible easier than ever. Manufacturers such as PCBgogo are offering low prices and high turnaround while maintaining a high quality of products. For instance, standard 2-layer FR-4 100x100mm PCB can be as cheap as $5 with 1–2-day delivery time.