Stickers have been around for a long time now. Although today you can make your own stickers at home. Professional sticker makers are still alive and kicking. And it’s because of the quality of work they put in their products. That is why many often wonder how they create such quality stickers. And if you are one of these people, then let this article be the one to answer your questions.
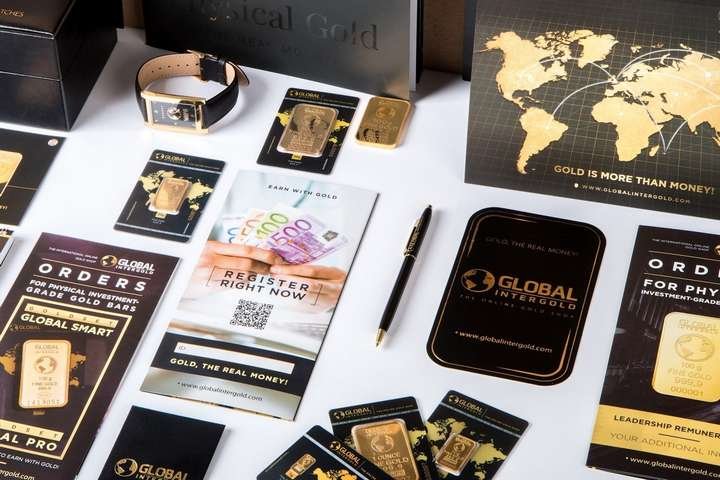
History of PVC (Polyvinyl Chloride)
People have been using PVC for hundreds of years. And it’s all thanks to Henri Victor Regnault, a French chemist, who discovered how to synthesize chlorinated carbons like polyvinyl chloride and vinyl chloride in 1895.
This opened doors for companies like Waldo Semon and B.F. Goodrich, taking the work of Regnault one step further and adding different additives to polyvinyl through experimentation, ultimately leading to the PVC we know today.
From PVC to Sticky Papers
“But wait, what does all of this have to do with a sticker?” Good question. You see, in the sticker business, you make quality stickers by converting PVC into flat sheets before getting it married to pressure-sensitive adhesive. If you want to get technical with the process, it’s the blending of sticky glue, which the decal industry likes to call “adhesive” and polymerized colorless gas.
After those sheets have been “married” you now have the printing material for all the quality stickers you want. But the fun doesn’t stop there. These sheets are not limited to just one thickness, size, or color. As you may know, white is the typical color when it comes to printing material. But if you take a look at the different stickers today, you will notice that they come in all different shapes, sizes, thicknesses, and colors. That is because some have been customized for necessity.
Customer Orders and Design
If you haven’t already realized, this is where you, the customer, come in. Logos, slogans, and different artwork by customers are sent to professional sticker makers to be colored and cut in various shapes and sizes so you can put them in cars, homes, walls, and more. If you are planning to make your own stickers, they’ll advise on the design too.
Overall, whatever message you convey with your stickers, they’ll ensure it will have the best quality and design.
The printing method of your sticker will depend on the kinds of art you sent. They’ll either choose digital printing or traditional screen printing. Both can make quality and durable stickers. It’s only the process where they differ.
If the sticker maker chooses a digital print for your sticker, they’ll send it as a file to the digital printer best suited for it. If the sticker maker uses traditional screen printing, they will run a film where a film image (your design) is burned to a screen. The screen will then press layer upon layer with different colors until the picture is complete. Once that is finished, production can then begin shortly.
Customizing Your Stickers
While the design may be everything when it comes to stickers, the shape and the ability to stick are also essential. That is why the back liner needs to be scored in the back of the sticker so you can remove them easily to expose the adhesive. If done poorly, you will have the tedious task of removing your sticker.
Your sticker needs to be cut correctly too. Depending on what is necessary, it will either be a clamshell die cutting machine or a digital machine that will cut your sticker. Each shape will have its design and intricacies, depending on what the customer wants.
Packaging
After all that, the stickers are packaged and shipped to the customer. They can now place them wherever they desire.
Conclusion
Stickers have always been used by many as one of the many tools to spread awareness and information. You can also use them to express creative designs and art. That is why you can still see stickers being used today. And a lot of things go through in creating quality stickers. So if ever someone is curious about how professional sticker makers make them, share this article with them.