GPR, which stands for “Ground Penetrating Radar,” is the most precise and non-destructive method that is used to mark and locate utilities. To ensure optimal results from the GPR surveys, you need to follow best practices regarding system setup, the right antenna, and target characteristics.
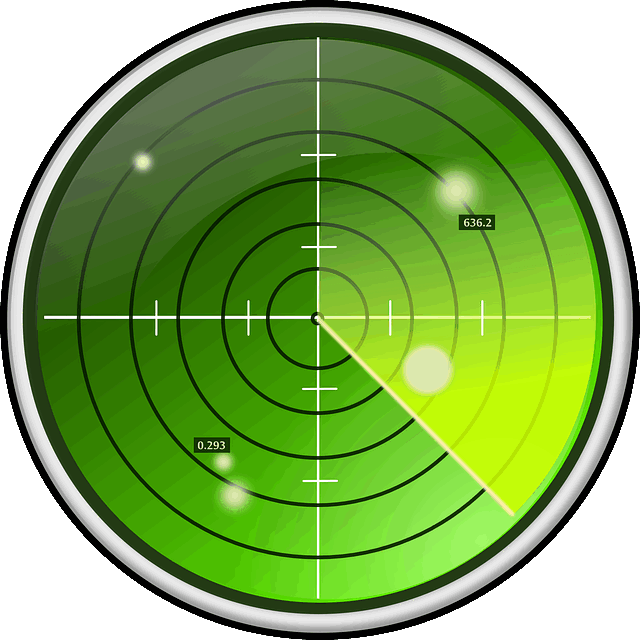
Know Your Target Characteristics
Before starting a GPR survey, it is important to assess the targets and any materials surrounding them with care.
GPR equipment is made to detect differences present in one or more materials. This can make surveying more complex when the materials share similar characteristics or how they react to the GPR signal.
The electrical conductivity relating to any of the surrounding materials will impact the depth at which the surveyor will be able to see.
PUM (Precision Utility Mapping) GPR Surveys are most useful for inspecting materials with a lower electrical conductivity, such as asphalt, wood, concrete, or sand. When it comes to conductive materials such as clay soil or wet concrete, the GPR energy will not penetrate as deeply into these materials.
In addition to the electrical properties of targets, other target characteristic types should be taken into consideration. This includes the orientation of utility lines, the size, and type, post-tension cables, or when there are other objects present like tanks or graves.
When considering the size of a target, the general rule for GPR is that this equipment can image targets with a size of one inch per 1 foot in depth. This means at a depth of 2 feet, the target would have to be at least two inches in size, or at a depth of 5 feet, the target would need to be 5-inches in size or greater.
Survey Design Considerations
In the instances where 100% confidence is required, the design of the Precision Utility Mapping UK has to include a “bi-directional grid,” and the space between each of the lines has to equal the smallest dimensions of every target.
When this isn’t a possibility, due to time or budget constraints, it is possible to use a larger overview grid, in addition to 1 or 2 smaller-focused grids. The “bi-directional grids” are better for investigating cylindrical objects like old buried oil tanks, drums, or complex utility areas.
The survey must use a 3D or 2D scanning method. With the 2D scans, the surveyor will collect individual basic profiles. This method will interpret and display the data on a “live” screen. Compared to 3D surveys, 2D surveys are much faster and easier.
With 3D scans, the surveyor uses a grid positioned across the ground. The scanner will collect the information along the parallel and perpendicular lines. From here, software, either in-office or an onboard-the-system, will take each profile individually and model them together, providing a top-down birds-eye view (similar to an MRI of the piece of ground).
The 3D bi-directional surveys are effective for targets that may move in unknown directions when absolute confidence is a requirement for the location of the target, when enhanced visual imagery is a requirement for a particular report, or when potential dangers may be present on the site.
The Right Antenna Will Make All The Difference
Selecting the right frequency for the antenna is essential when it comes to obtaining accurate information for GPR target locations. The antenna type chosen will rely on the size and depth of a target, along with the material-imaging through. Low-frequency antennas like those 200 MHz or lower allow an operator to view targets a bit deeper, yet the resolution will start to decrease. Targets must be large enough to be seen and detected.
When it comes to scanning utilities, a “mid-range antenna” is usually a better option. For instance, GSSI developed a new technology that they named “HyperStacking” to view deeper targets and the ability to operate in conditions that are “too noisy” for conventional systems.
The antenna design includes a new accessory that helps to locate precise power sources. This new technology also can detect power that radiates from electrical cables or induced radio frequency and fuses all this with GPR data on one display.
When it comes to the radar data, the user can also produce overlays that show if there are specific pipes present. Most of the GPR systems will also include GPS integration. This is frequently used for providing local information in the radar-data file.
System Setup Is Essential
Operators must ensure these systems are set up correctly by selecting the correct depth level. The right scan numbers also need to be collected to obtain data density to accurately find what a surveyor is looking for. It is recommended to begin with the as-built plans that usually display site features indicating pipe location or orientation, such as manholes or basins.
The boundary of a site survey also needs to be set correctly to capture what is required. The right scan numbers can vary according to characteristics such as the soil, the target’s size, and any other materials present. Smaller scan spacing (more than 1 scan per unit) slows surveys down. This is why it is better to collect higher scan numbers while retaining acceptable survey speeds.
Small targets typically require higher numbers of scans. For example, if a target is only 1-inch, it will take a minimum of 2 to 3 scans per inch, as this increases the chances of hitting a target.