An actuator is a mechanical device that converts energy into linear or rotary motion and is commonly used to turn valves. There are seven types of actuators, covered in detail in this article: manual, manual geared, electric, pneumatic, hydraulic, solenoid, or spring. Each actuator type finds specific use depending on the application. This article gives the reader an overview of major actuator types and functionality.
Manual Actuators
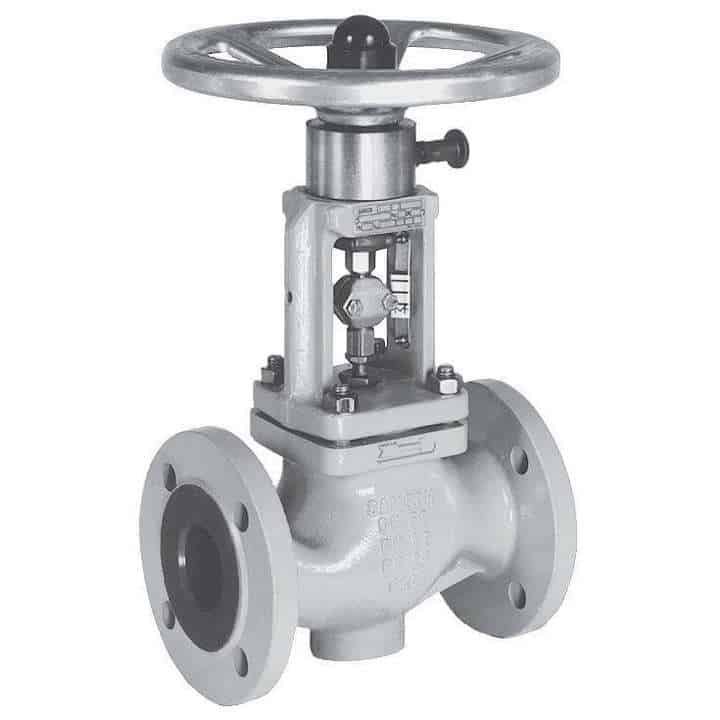
Manual actuators enable movement by utilizing gears, wheels, or levers. They are hand-operated and straightforward to use. Manual actuators are ideal for the following conditions: unrestricted, low damper/valve quantity, reasonable operator input requirements, safe environment, and infrequent use. In toxic, remote, and classified environments, a different type of actuator is recommended due to accessibility concerns. Also, specific process requirements may require quicker operations than physically possible via a manual actuator.
Actuation may be accomplished via a handle, hand wheel, chain wheel, or manual gearing. Manual geared actuators provide a mechanical advantage and may be characterized independently.
Manual Geared Actuators
Manual gear actuators utilize an additional gear train to allow easier turning capability. As a result, torque and performance are increased, and speed is reduced. Operational life in gear actuators is extensive due to overdrive prevention. Gears can be configured to fit many partial-turn/multi-turn valves to reduce the work required to cycle a valve. Extra friction, inertia, or sharp load changes may occur when a manual geared actuator is used.
Electric Actuators
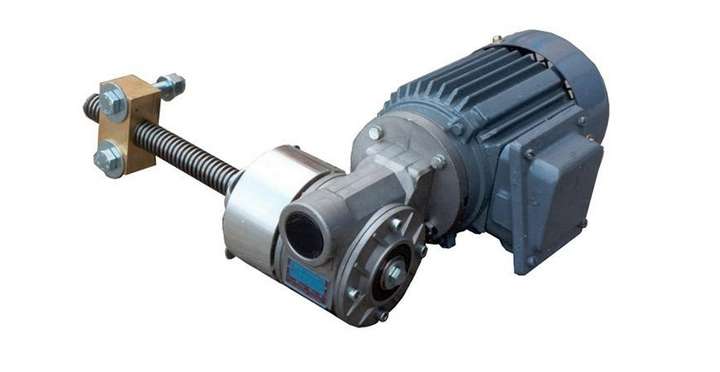
Electric actuators rely on motor rotation to produce torque. Common electric actuators vary in dimension/size and are non-toxic, quiet, safe, and energy efficient. They require readily available electricity or batteries for performance. Typical uses are industrial valves and technical process plants (e.g. power plants, oil and gas plants, wastewater treatment plants).
Pneumatic Actuators
Pneumatic actuators are powered by air or gas pressure, converting energy into rotary/linear motion. Air pressure acts on a piston/bellows diaphragm that applies linear force on a valve stem. They are highly reliable, efficient, and safe sources of motion control. Common applications include pistons and ignition chambers in gas-powered vehicles, air compressors, packaging/production machinery, and transportation equipment. Variable speed control and slow movement are difficult with pneumatic actuators. Periodic pressure testing/leak checking is also required.
Hydraulic Actuators
Hydraulic actuators convert fluid pressure to mechanical energy to produce linear or rotary motion. Hydraulic actuators are generally used for linear movement to control valves. Most hydraulic actuators have fail-safe features that close or open a valve in emergencies. They operate similarly to pneumatic actuators but utilize incompressible liquid from a pump instead of pressurized air. Hydraulic actuators provide high accuracy movement/control and are commonly used when high speed and large forces are required. However, they are dirty to operate, and leakage is common. Usage is typically seen in industrial process control and transport applications. Hydraulic actuators are also the most expensive option.
Solenoid Actuators
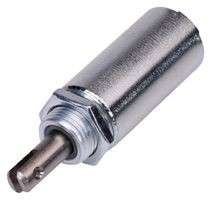
Solenoid actuators convert electrical signals into mechanical linear motion. Made of a movable coil and iron core, a solenoid’s pushing and pulling strength is determined by the number of coil turns. A major aspect of the solenoid is a small jolt that produces a high level of operation with little power required. If the current flows, the coil pushes the core to open the channel/valve. No flow results in a closed channel. Typical solenoid applications include Linear applications, latching/switching, sorting, and fuel injectors. Solenoid applications are not typically used in large bore applications.
Spring Actuators
A spring-based actuator holds springs in place that operate a valve when an anomaly is detected (e.g., power is lost). These types are desirable where power failure can compromise a system. When an actuator loses power, air supply, or hydraulic pressure, the springs expand to return the actuated component to its original position (fail position).
These only operate once, without resetting, and are typically used for emergencies. Spring actuators do not require an electric supply to move the valve and can operate from restricted battery power or mechanically if all power dissipates.
How to Choose the Right Actuator for Your Application
Mismatched applications cause a great deal of inconvenience and even can impede a system’s functionality completely. For example, a manual actuator may not even be able to operate if the valve’s break torque values are too high. Specialty valves such as the Orbit valve or butterfly valve may require a specific actuator.
Generally, users should consider break torque, reliability requirements, available power, duty cycle, and the application before specifying an actuator.