In the field of prototype creation, metal stamping is a cornerstone that is essential to many different sectors. This method, which forms and shapes metal sheets using a press machine, is important to producers and designers. Metal stamping is a key process in making prototype designs a reality because of its capacity to guarantee accuracy, economy, and quick prototyping. Understanding the foundations of metal stamping allows for increased productivity and creativity while creating prototypes.
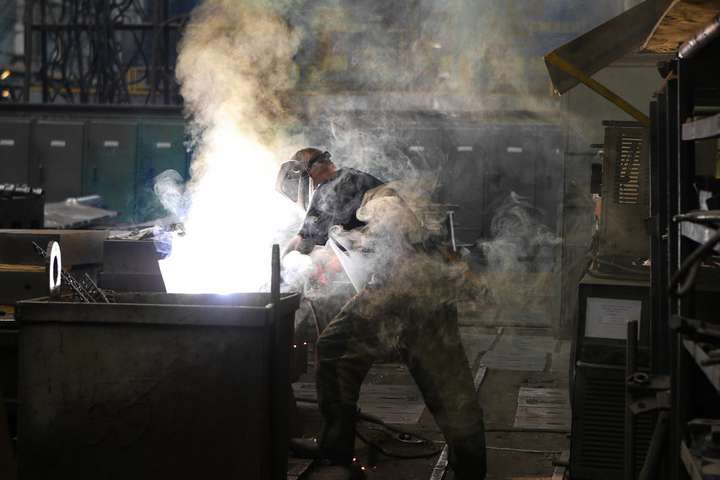
Overview of Metal Stamping for the Creation of Prototypes
Metal stamping is a basic method used in many industries to create prototypes. It involves utilizing a press machine to shape and size metal sheets into the proper shapes and sizes. Prototype parts must be produced precisely and consistently using this process to be tested and validated. Metal stamping provides material selection adaptability, meeting various application needs because of its versatility in working with different metals such as copper, steel, and aluminum. Furthermore, metal stamping’s affordability makes it a desirable choice for prototype projects with limited funding, allowing producers to create parts quickly and affordably.
Accuracy & Precision
Each component is painstakingly made with attention to detail thanks to the precision and accuracy process, which provides consistent and uniform outcomes. Manufacturers can meet the necessary criteria for prototype components by achieving elaborate designs and precise tolerances through the use of specialized tooling and processes. Maintaining exact measurements and forms is essential to guarantee the finished product’s performance and usefulness. Designers can trust the quality and dependability of their prototype parts thanks to metal stamping, which makes testing and validation procedures more efficient.
Expense-effectiveness
A cost-effective manufacturing method is the method of choice for projects with limited budgets because it can produce parts in large quantities at a lower cost per unit than other approaches. Manufacturers may keep quality standards high and production costs low by utilizing effective processes and tooling. Prototyping at a reasonable cost allows designers to experiment with different design iterations and enhance concepts without going over budget. Cost-effective metal stamping solutions also help projects become more affordable overall by accelerating the time it takes for new items to go from concept to market and development.
Flexibility in the Choice of Materials
One of the main advantages of using metal stamping to create prototypes is the versatility of material selection. It is possible to deal with a variety of metals, such as copper, steel, and aluminum, using this procedure. Based on certain application criteria, such as strength, conductivity, or corrosion resistance, designers are allowed to select the best material. Prototype parts can be more customized and optimized with a wider selection of materials, guaranteeing that they fulfill the endurance and performance requirements required for testing and assessment. Furthermore, metal stamping is flexible enough to handle a range of material compositions and thicknesses, giving designers the freedom to experiment with various prototypes and design ideas.
Quick Prototyping
Manufacturers can shorten lead times and speed up product development cycles by producing prototype components quickly with effective tooling and setup techniques. Designers may test and refine various design variations more quickly with metal stamping, which speeds up prototype optimization and refinement. This quick turnaround time improves the prototyping phase’s agility and reactivity, allowing designers to address design difficulties and make required revisions quickly. Furthermore, prototype parts are consistently reliable and of high-quality thanks to the efficient metal stamping production process, which facilitates efficient testing and validation activities.
Suitability for Large-Scale Manufacturing
One of the main benefits of metal stamping when creating prototypes is its scalability for mass production. Metal stamping manufacturers can quickly modify the same tools and procedures for mass production after the prototype design is finalized. The manufacturing process is streamlined by this smooth transition from mass production to prototyping, which lowers costs and boosts productivity. The capacity to consistently and reliably create huge volumes of parts using metal stamping satisfies the needs of large-scale manufacturing operations. Manufacturers may efficiently fulfill market demand and scale production under company demands by utilizing the scalability of metal stamping, guaranteeing prompt product delivery to clients.
Conclusion
It is an essential approach for both designers and manufacturers due to its accuracy, affordability, and speed of prototype. Prototype development is made more effective and dependable by metal stamping’s scalability for mass production and versatility when working with various materials. Embracing the advantages of metal stamping reduces development time from concept to final product and opens up new creative avenues.