In 1860, Jacques E. Brandenberger discovered that carbon fibers could be produced by passing an electric arc through dry carbon dioxide gas. This method of producing carbon fibers is still in use today. The first person to manufacture carbon fiber was Leo Baekeland, who manufactured charcoal at high temperature and pressure, then passed an electric current to produce carbon fibers.
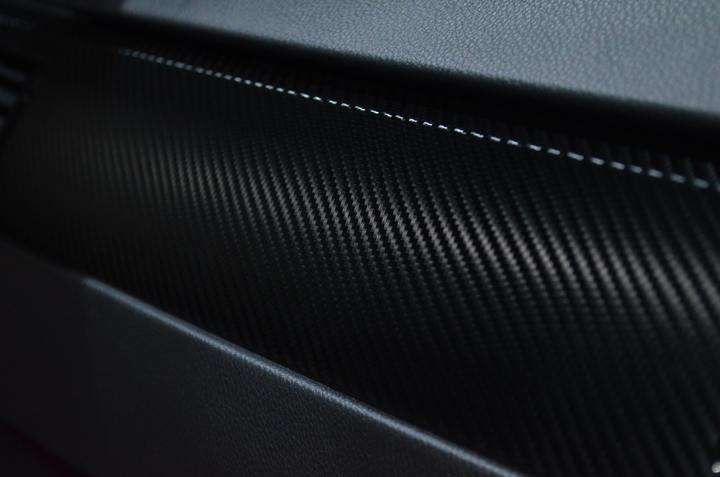
In 1911, D. G. Comyn patented a method for spinning carbon fiber. Comyn was able to produce fibers that were not only stronger than natural fibers, but also had exceptional flexibility.
In 1924, Paul Moody developed a process for spinning carbon fiber. This method is still in use today.
In 1956, Roger Bacon created a process for making carbon-fiber tapes that could be used in the aerospace industry.
In 1958, the first commercial shipment of carbon fiber occurred.
In 1966, the first carbon-fiber reinforced polymer (CFRP) composite material was produced.
In 1977, a patent was issued to Charles W. Hull for a process for spinning carbon fibers.
In the late 1990s, carbon fibers were being produced with tensile strengths from 14,000 to as high as 56,000 MPa (20 to 80 GPa), tensile moduli of 70 to 110 GPa, and specific strengths (tensile strength per unit weight) from 0.1 to 1.4 GPa·m/kg.
Compared to steel, carbon fiber is lighter and stronger, and much more elastic (i.e., resistant to permanent deformation). This is why you often find carbon fiber plates in fabric. Carbon fiber is also stiffer than steel and can be made much more so by introducing defects (i.e., deliberately changing the direction of the fibers) into the carbon-fiber structure. The material is highly resistant to fatigue, in some cases twice as resistant as steel. However, it is lightweight, has high strength, and is very stiff. The higher the tensile strength of carbon-fiber material, the stiffer it is. In most applications, the stiffness of the material is more desirable than its strength.
The overall properties of carbon fiber (strength, stiffness, elastic modulus, etc.) are dependent on the type of carbon fiber, the type and degree of graphitization, the orientation of the fiber, the weave, and the matrix material in which it is embedded. The properties of the carbon fiber depend on the type of carbon source used. This is because turning a source of carbon into a filament of carbon fiber involves several steps. Each of these steps alters the structural and/or chemical properties of the fiber.
Carbon fibers are made by a process called carbonization. During carbonization, a carbon source (typically a hydrocarbon) is heated to high temperatures (typically about ) under an inert atmosphere (typically nitrogen or argon) and in the absence of any oxygen. At this temperature, the source undergoes a process known as pyrolysis, which produces a liquid and gaseous product. The liquid product is referred to as “synthesis gas” or “syngas.” The gaseous product is referred to as “coke.” The coke is referred to as “calcined coke” when subjected to temperatures greater than in a furnace.
The coke is then allowed to react with steam (or occasionally water) to produce the final product. The coke may be reacted with steam at a temperature ranging from, depending on the desired properties of the final product. The process of coke reacting with steam is referred to as “coking.” The coke may be reacted with water at or near ambient temperature. The water may be added to the coke before or after the calcination process.
Typically, the amount of water is in the range of 2–15% by the weight of the coke. The amount of coke used maybe 80 kg for every 1 kg of water added.
In a typical carbonization process, the coke would be added to a high-temperature reactor, where it would be carbonized. The carbonization process may be exothermic, and the reactor will be designed to allow the heat to escape. The gaseous products of carbonization will be allowed to flow through a condenser and condense into a liquid. The liquid product will be separated from the gaseous products. The liquid product is the “syngas,” and the gaseous products are the “recycle gas.” The syngas is then fed into a furnace, where it is allowed to react with steam to produce the final product.
The carbon fibers have a diameter of about 5–10 micrometers and a length of several centimeters. The fibers are fragile and are separated by a thin layer of the matrix material. The fibers are typically arranged parallel to each other. The length of the fibers may be altered by drawing. The fibers are usually bundled together to form a yarn. The yarn may then be used to form a fabric. The fabric may then be cut into smaller pieces of various dimensions.
Carbon fibers may be turned into a “mat” or “roving.” The roving may be used to create an object, such as a composite material or a textile. The roving may be impregnated with a matrix material, such as a polymer or a metal. The impregnated roving is then heated to high temperatures and then allowed to cool, which causes the matrix material to harden. This process is known as curing. The impregnated roving may be applied to an object and then heated to a high temperature. The high temperature causes the impregnated roving to harden and form a matrix around the object.