Pipelines are widely used to transport oil or gas from one point to another for user consumption. Miles and miles of pipeline systems have been constructed for the past years, and more are still being constructed.
But pipeline operations can be a challenge as operators need to ensure that environmental health and safety risks are addressed. These risks should be considered starting from selecting devices to be used to construct the pipelines.
Even a small leak in the pipeline system can cause a disaster that can sever humans’ well-being and the environment.
But no need to worry as we will discuss some key factors you should consider in oil and gas pipeline operations. So if you want to know more, read this article. #1 Consider the Thickness of the Pipe Walls
#1 Consider the Thickness of the Pipe Walls
The thickness of the pipeline walls plays an important role in reducing the risks of pipeline disasters. It also mitigates the cost of the whole pipeline project because the project timeline is shortened.
Weak pipe walls are the most common problems regarding pipeline failures that cannot support heavy loads or stress. This causes corrosion, leak developments, material defects, and natural hazards.
Before organizing a pipeline design and calculating pipe wall thickness, you first need to determine the appropriate codes and standards because the design factors and formulas in calculating wall thickness vary for each code and standard.
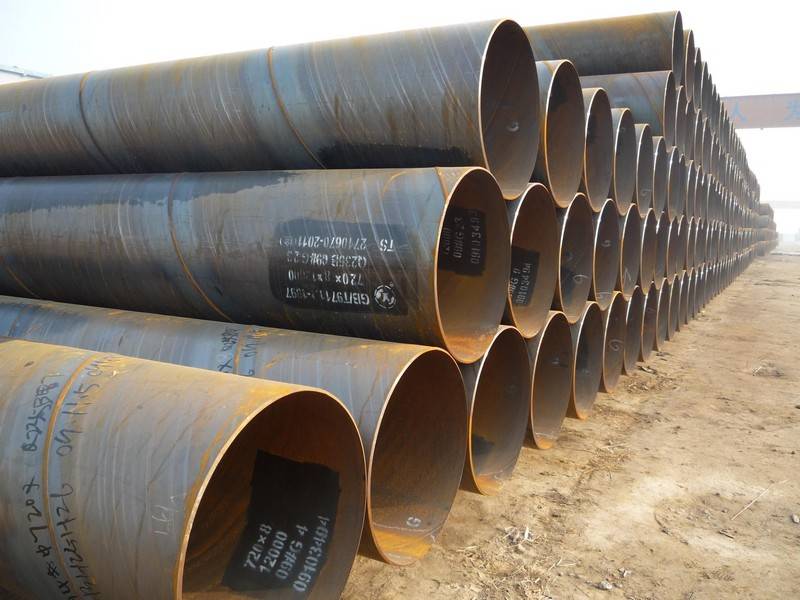
The existence of railways, marshlands, railways, flooded and hydraulic shock areas and other distractions should also be considered. These factors affect calculations of strength and stress that, in turn, impact calculations for wall thickness. Thus, the requirements for the appropriate thickness of the pipe walls are affected by many factors, which include:
- Pressures
- Temperatures
- Chemical properties of the oil/gas
- The velocity of the oil/gas
- Volumes being transported
- Location of the pipe
- Grade and material of the pipe
- The code design application
#2 Consider the Pipe and Joint Coatings
The quality of the provided and maintained protection by an oil and gas industry reflects the integrity of the industry’s infrastructure. The design and selection of the appropriate coating for pipes and joints also depend on many factors. These include weather conditions, flow rate and physical state of the materials traveling through the pipe, flammability, and viscosity.
You also need to consider the location of the pipe or joint, whether it is underwater, underground, or above ground. So the coating needs to be formulated so that it provides long-term durability, internal and external.
Let us discuss the factors in coating formulation further and the things that you should always remember:
- First, the formulation should withstand diverse temperature and climate. Do not also forget the physical location of the pipes.
- Second, the physical state of the material transported through the pipes have impurities and can become abrasive at high-speed flows. So the coating should be highly resistant to varying particulates at high-speed flows.
- Third, the coating should also be appropriate for different fluid viscosities.
- And lastly, the flammability of both the coating and the oil/gas transported through the pipe should also be considered.
#3 Selecting an Appropriate Pump or Compressor
Choosing the appropriate pump or compressor for your pipeline system can also help avoid pipeline failures. Pump/compressor stations are crucial to the transport system as they enable the oil/gas to travel through the pipelines. But first of all, you should know that a pump is different from a compressor. A pump moves a fluid, may it be liquid or gas, from one point to another. In comparison, a compressor squeezes only gasses as it travels through the pipelines.
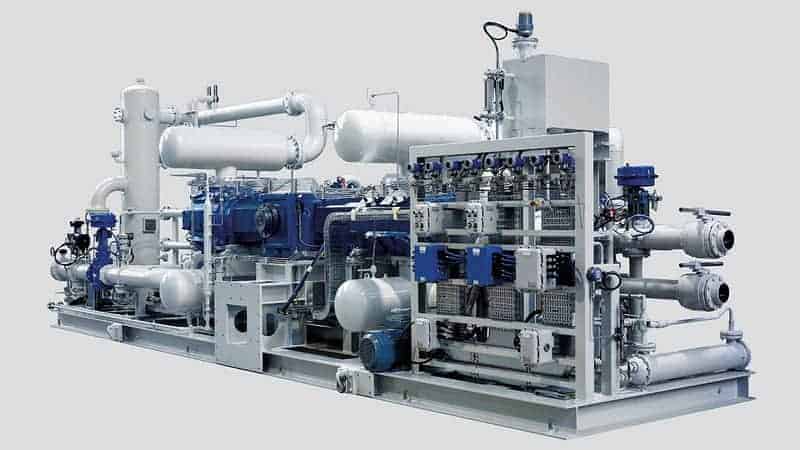
Always consider pump and compressor stations as part of the pipeline system as they are not independent systems. The design of the pump/compressor depends on the composition and properties of the fluid, minimum and maximum flow, and pressures.
There are different types of pumps and compressors designed for different applications. The selection not only depends on the application but also the driver used for the pump/compressor. It would be best if you educated yourself more about pump and compressor operations.
#4 Selecting a Reliable Valve
Valves are installed in block valve stations which are along the pipelines. They allow operators to turn off sections of the pipeline system for maintenance or during emergencies.
Moreover, valves are used to control and regulate the flow and pressure of the fluid passing through the pipelines. This makes them a crucial part of the pipeline system and should withstand punishing conditions. That is why finding a strong and reliable pressure and flow control valve for your pipelines is a must.
The most commonly used valves in pipeline systems are start/stop valves and throttle or flow control valves. Start/stop valves, as the name implies, allow or block the flow of fluid. These are further categorized into the gate, rotary ball, and plug valves. But gate valves are mostly used in pipeline operations. And if you are looking for a reliable strainer manufacturer, check out XHVAL.
Contrarily, throttle or flow control valves are used to control the pressure and speed of fluid flow in a system. These are butterfly, diaphragm, globe, needle, pinch, and squeeze valves. You can find detailed descriptions of the differences between the mentioned valve types here.
#5 Leak Detection Systems
Lastly, this is the most critical thing to consider when constructing a pipeline system to maintain pipeline integrity. As mentioned above, leaks have been a major problem in pipeline systems and have caused disastrous results. Not only is it a threat to people’s safety, but it is also harmful to the environment.
The most common alternative used by operators was manual inspection and detection through walking, driving, or flying over the pipeline. So, consider a detection system that avoids risk during operations and guarantees safety during the addition or expansion of plants. In the same way that the water industry has been revolutionized by implementing active water leak detection systems that can pinpoint water network leaks, the same can be applied to the gas and oil industry.
The following are some of the criteria that you can consider when looking for a leak detection device:
- detects even the smallest leaks
- detects both liquid and gaseous leaks
- identifies possible points or failure properly
- manages pressure control/protection systems
- monitors corrosion or erosion
- monitors the whole area non-stop, 24 hours a day
- should be able to trigger shutdowns automatically, and
- avoids risks while keeping running costs low
So instead of using a person to monitor leaks, you can look for a leak detection system available in your area. And it should conform with industry standards and regulations.
Conclusion
So that’s it! Pipeline operations are very challenging, but having the right knowledge to choose the appropriate materials can help. This helps in disaster management and mitigation and ensures the integrity of the industry infrastructure. We hope that the mentioned tips will help you choose the right materials for a successful pipeline operation.