Teledyne Hanson was established in 1951 and quickly earned the trust of laboratory workers involved with pharmaceutical development and quality control through their reliable, precise, and user-friendly dissolution testing instruments such as their Vision G2 Elite 8 and Classic 6 dissolution testers that meet or surpass all others on the market – but that’s not all they’re about.
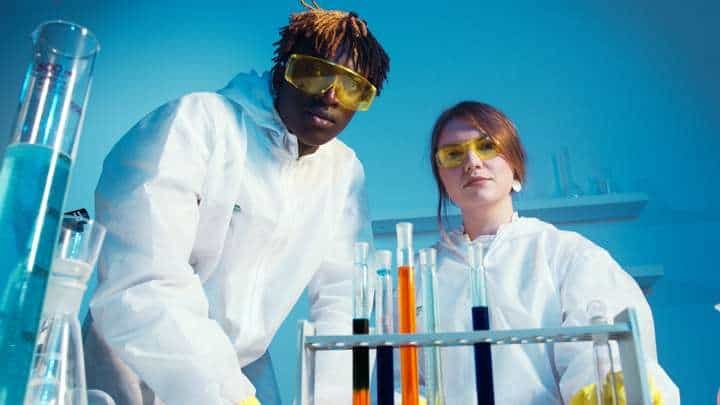
Dissolution Testing
Dissolution testing is an in vitro evaluation that measures how an active pharmaceutical ingredient (which you can read about here) dissolves in the solid dosage form. It’s used throughout drug development to monitor changes to both API and formulation products, as well as reduce in vivo bioequivalence studies or clinical trials. Dissolution testing plays an integral part in the quality and performance assurance of drug products, helping ensure quality and performance are at their optimal.
Dissolution tests should be robust and reproducible in order to highlight or discriminate key changes in formulated products. Therefore, it is crucial that dissolution methods be tailored specifically for your desired conditions (dissolution medium and apparatus), with no artifacts and low to moderate variability; challenging enough to identify key quality attributes and discriminate between formulations.
Hanson Research dissolution testers include the Vision Classic 6 and Vision G2 Elite 8 models – reliable workhorses that meet regulatory requirements for USP, EP, JP, CSA, RoHS, and 21 CFR Part 11. Both provide high precision in measurements with an attractive aesthetic design making them suitable for pharmaceutical development and manufacturing laboratories.
They remain one of the industry leaders when it comes to dissolution testing equipment for pharmaceutical and biotech manufacturers worldwide for a reason. Their quality assurance equipment used for release rate testing, stability monitoring, and control can be found in over 75 countries around the globe. Hanson combines pioneering research, innovative technology, and top-tier customer support in order to consistently produce excellent results that enable their pharmaceutical and biotech clients to meet product and safety goals with confidence.
Diffusion Testing
Diffusion testing is a quick, noninvasive test to measure how effectively your lungs allow oxygen and carbon dioxide to pass into and out of the blood. Doctors use diffusion testing in combination with other pulmonary function tests to diagnose or monitor lung diseases.
A doctor will use a mask on your face while pumping in the air tracer gasses like helium or carbon monoxide into it – this tests the speed with which they move from your lungs into capillaries surrounding the alveoli into blood capillaries nearby and measures diffusing capacity or DLCO capacity or diffusing capacity or DLCO capacity (DLCO).
Your lungs consist of several components, including the trachea (windpipe), bronchioles, and alveoli sacs. When breathing in, these organs move oxygen from your mouth and nose into the capillaries via diffusion; when their ability to transfer oxygen and carbon dioxide reduces, respiratory conditions may arise as a result; diffusing capacity testing helps healthcare providers assess the severity and monitor treatment progress of such conditions as well as monitor treatment progress over time.
The DB-6 manual sampler offers six cells in a compact footprint for flexible system configuration. However, for labs seeking automation, Teledyne Hanson offers the Phoenix RDS automated system with up to 24 diffusion cells at one time. Both systems use Protocol Manager software for easy set-up and operation while offering you flexibility as your needs change in the future expansion of your system.
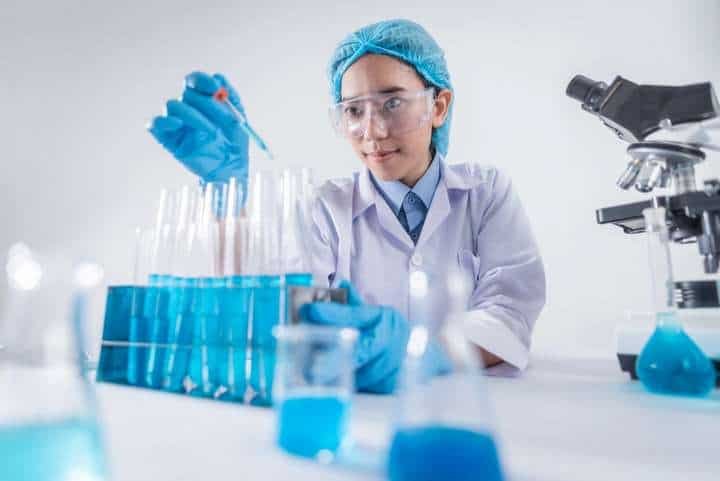
Physical Testing & Other
Physical testing is a technique for evaluating products or their components to ascertain their specific properties such as density, surface area, and weight. These properties help ensure the material meets its intended use safely. Physical testing can be found in fields like physics engineering and quality assurance – but here, we’re talking about pharmaceuticals.
Pharmaceutical powder flowability has an enormous influence on manufacturing efficiency – such as how quickly tablet presses can run – as well as product quality measures such as dose uniformity. Unfortunately, our current knowledge about what influences powder flowability remains limited to statements rather than quantified correlations, even for key variables such as particle size and shape.
Manufacturers need reliable and repeatable methods of characterizing the flowability of pharmaceutical powders in order to be certain they can be used safely in production. A number of different tests exist that meet this criterion, including USP recommended angle of repose tests (https://iopscience.iop.org/article/10.1088/0305-4470/26/2/021) which measure the constant three-dimensional angle formed by cone-like piles of drug powder forming piles.
Manufacturers of pharmaceutical, over-the-counter, and dietary supplement products must ensure that their products meet all relevant regulations, such as meeting the FDA’s stringent standards of identity, assay, and stability.
Stability testing is an intensive procedure designed to assess your drug’s chemical, physical, microbiological, and therapeutic properties in terms of chemical reactions, physical characteristics, microbe counts, and therapeutic efficacy. It allows you to establish factors like shelf life, storage conditions, and retest periods, as well as detect any degradation which might compromise its efficacy and safety for consumers.