The sun is essential to all life on earth; we simply wouldn’t be here without it. Its energy and heat have been driving all our life processes for millions, if not billions, of years.
There’s a few downsides to the sun’s rays through. The UV light that helps insects and birds see things we can’t, gives us a glowing tan, and even helps to kill viruses can also cause damage. This damage can occur to living cells and inanimate objects and equipment. We see it, for example, if we look at a pair of curtains in a south-facing window – they’re bleached over time by the sun. The UV light has altered the chemical structure of the pigment in the cloth, which becomes lighter as a result.
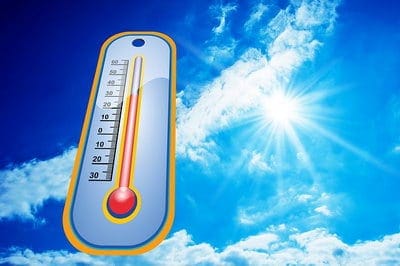
UV light can also alter DNA, which is handy for killing viruses, and helping to bring about positive mutations in plants and animals, but it also causes sunburn and cancers. A double-edged sword indeed.
Too long in the sun
A less-obvious effect of long-term UV exposure is seen in some industries, too. The oil and gas industry needs large structures to operate – offshore platforms and massive pipelines and cables, for example.
These structures are intended to stay put for a long time – decades, even – and while some pipelines are submerged or buried underground, some have to be above the ground. Pipelines that are above ground tend to be made from highly reflective metals, so sunlight bounces off them, while undersea pipes and cables are made from lightweight but resilient plastics.
Once installed underwater, these pipes receive little UV light, but problems can occur during storage. Pipes can be manufactured a long time before deployment, and if they’re stored outside, especially in a hot or even a Polar region, high levels of UV light will start to damage them. The walls of the pipes become significantly thinner, especially along the tops, as these take the brunt of the midday sun. They can also lose flexibility and become more prone to cracking under stress.
Some oil and gas projects need several hundred or even several thousand kilometers of pipeline, so if a significant proportion of these pipes is no longer fit for purpose or safe, the damaged pipes will have to be replaced at a high cost. Damage can also cause delays to the start of extracting and moving oil, which, again, adds considerable costs to a project.
Take cover
One proven solution to this problem is to have customized protective covers for the stockpiled pipes. If the oil company knows there will be a few months or a year before the pipes are deployed, then the covers can be ordered and made in advance from suppliers like Cunningham Covers. Sometimes however, there’s an unexpected delay to the start of a project, and the pipes may have to be left at the side of a port until usage. This is where customization is a huge help – UV-protective covers can be made to fit the piles and be delivered to them in a matter of weeks, long before the UV light really starts to affect the pipes’ strength and flexibility.
Compared to the cost of replacing damaged pipeline, a made-to-measure UV-protective cover is a positive addition to the balance sheet.