Railways keep people and goods moving day and night, and every safe journey begins with well-cared-for tracks. In the past, crews relied mostly on manual labor, which was slow and exhausting. Today, a wide range of easy-to-handle power tools has changed the game, helping workers finish jobs sooner, with less strain, and with higher accuracy. Below are four key ways these tools make a difference out on the line.
Power Tools Keep Tracks Safe
When trains speed across steel rails, even tiny flaws can grow into big risks. Portable grinders, drills, and impact wrenches let crews spot-fix bolts, clips, and worn rail heads before trouble strikes. Because these handheld machines are light yet strong, teams can carry them to remote spots and get straight to work without waiting for heavy equipment.
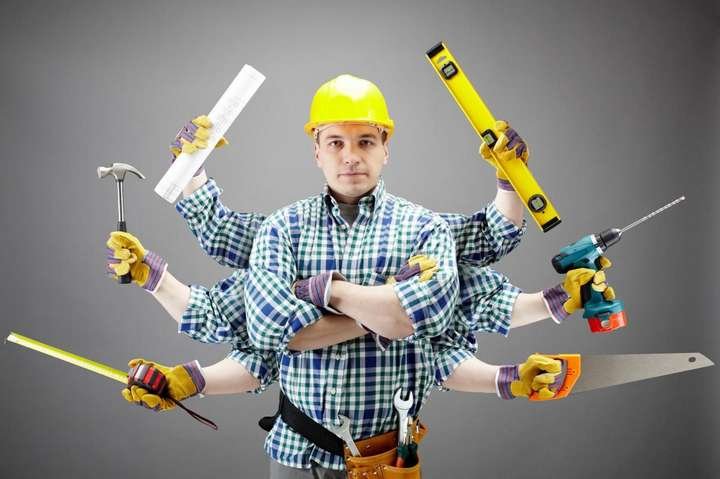
A quick pass with a grinder removes sharp edges that could crack, while a cordless drill tightens loose fasteners in minutes. By shortening repair time, power tools reduce the hours that tracks stay out of service, keeping passengers and cargo rolling safely on schedule.
Speeding Up Day-To-Day Upkeep
Regular upkeep—checking joints, tightening plates, and replacing sleepers—used to eat up full shifts. Now, battery-powered screwdrivers and saws mean crews cover longer stretches in less time. One worker can slice through old wooden ties cleanly, while a teammate installs fresh ones with a driver set to the right torque.
Rechargeable batteries last an entire shift, and swapping packs takes seconds, so there is no long wait for generators or cables. Faster daily tasks free teams to focus on bigger projects, like replacing bridges or revamping stations, without staffing extra shifts or causing major delays.
Cutting And Joining Made Simple
Spare rails must match perfectly with the existing line, and cuts have to be straight and smooth. Rail saws with diamond blades give a neat finish in one sweep, trimming metal with less noise and fewer sparks than older gas torches. Once pieces fit, hydraulic clamping tools press them together tightly, creating joints that stay firm under the pounding of passing wheels.
The same tools help welders bond the rail ends quickly, forming near-seamless tracks that ride smoothly and cut down on wear. By turning a once-difficult task into a straightforward process, power tools let maintenance crews reopen sections sooner and lower the chance of future loosening.
Supporting Workers And Cutting Costs
Power tools are not just faster; they are kinder to the people using them. Lightweight casings and cushioned grips cut down on back strain and hand fatigue, leading to fewer injuries and less sick leave. Simple push-button controls reduce training time, so new hires become productive quickly.
Because jobs finish faster, rail operators spend less on overtime and can schedule maintenance during quieter hours, trimming lost revenue from service stoppages. Over months and years, these savings add up, helping railway companies invest in better facilities and more frequent inspections, further lifting overall safety.
Conclusion
From tightening a stubborn bolt to slicing through a damaged rail, modern power tools have become the quiet heroes of railway maintenance and repairs. They help crews work faster, safer, and with greater care, ensuring that the tracks beneath every train stay strong and steady.
As technology keeps advancing—lighter batteries, smarter motors, tougher blades—the partnership between skilled workers and reliable power tools will only grow, delivering smoother journeys for everyone who rides the rails.