Sewage treatment plants sit quietly at the edge of our cities, doing the unglamorous work of turning murky wastewater into something clean enough to release back into rivers or seas. Yet the task is becoming tougher by the year. Populations swell, industries discharge new chemicals, and extreme weather sends sudden deluges through pipes never meant to carry such loads.
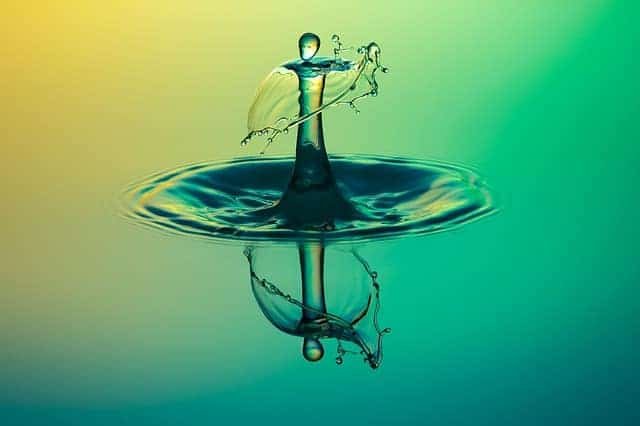
In response, engineers and plant managers are rethinking everything from hardware to staffing. Below are four key areas where challenges pile up—and where promising advances are starting to break through.
Aging Infrastructure and Capacity Strains
Many treatment facilities were built decades ago, when today’s volume and mix of contaminants were unimaginable. Concrete basins crack, steel corrode, and outdated grit screens struggle with wipes and plastics that never should have been flushed. Operators must keep these aging workhorses running while simultaneously planning expansions or retrofits to add capacity.
Modular clarifiers, drop-in membrane units, and high-rate settling tanks are emerging as fast ways to squeeze more throughput from small footprints, buying time until full-scale upgrades can be funded.
Tightening Environmental Regulations
Regulators now demand effluent so clean it borders on drinking-water quality, setting low parts-per-billion limits for nutrients, microplastics, and trace pharmaceuticals. Meeting these targets can double or triple energy use if plants rely only on legacy aeration or chemical dosing.
Advanced oxidation processes—think ultraviolet paired with hydrogen peroxide—and anammox-based nitrogen removal are helping cut both emissions and power bills. Some facilities even sell recovered phosphorus as fertilizer, flipping a compliance cost into a modest revenue stream.
Skill Gaps and Operational Efficiency
Running a modern plant takes more than rotating valves and reading gauges. Staff need to understand data analytics, microbiology, and power management—skills in short supply as seasoned operators retire.
To bridge the gap, utilities partner with technical schools, offer virtual-reality simulators for training, and deploy user-friendly SCADA dashboards that highlight anomalies before they become emergencies. These tools free personnel from constant firefighting and allow them to optimize processes, trimming chemical use and cutting sludge volumes.
Integrating Smart Technologies and Energy Recovery
Digital twins, machine-learning algorithms, and the Internet of Things are no longer buzzwords—they are practical tools that predict influent surges, adjust blower speeds, and schedule maintenance before parts fail.
For example, overhung (OH) and between bearings (BB) pumps now ship with built-in vibration and temperature sensors that feed performance data to cloud platforms, letting crews plan repairs during low-flow windows instead of scrambling after a breakdown. At the same time, plants capture biogas from anaerobic digesters to run micro-turbines, producing electricity and trimming grid dependence.
Conclusion
Sewage treatment may never become glamorous, but it is evolving rapidly under pressure from aging assets, stricter rules, workforce shifts, and sustainability goals. By blending smart monitoring, modular upgrades, and resource recovery, today’s plant operators are turning challenges into stepping-stones toward cleaner water and greener energy—all while keeping the public blissfully unaware that their flush is part of a much bigger story.