HDI PCB stackup is a multilayer printed circuit board (PCB) that uses high-density interconnects (HDIs) to connect its various layers. HDI technology allows for smaller and more densely packed circuitry than traditional PCBs, making them ideal for use in space-constrained electronic devices.
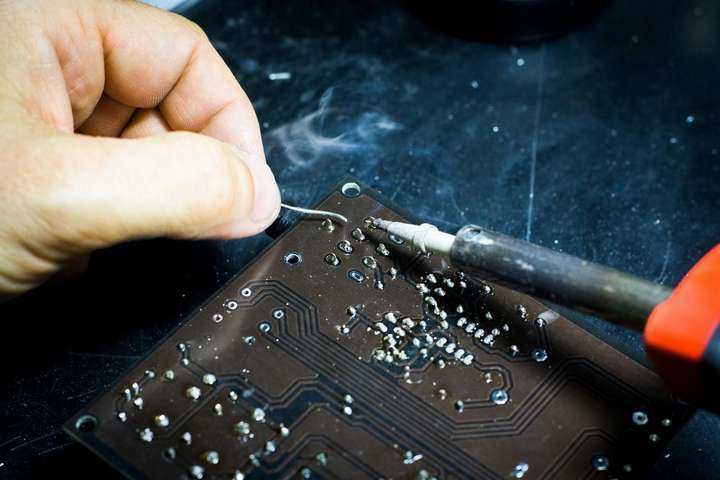
HDI PCB Stackup
The typical HDI PCB stackup consists of four layers: a substrate, a dielectric layer, a conductive layer, and a solder mask.
Substrate
The substrate of an HDI PCB stackup is one of the most critical aspects of the design. The substrate material must have a dielectric constant compatible with the signal integrity requirements of high-speed digital circuits. In addition, the substrate material must have good thermal conductivity to dissipate heat from the high-speed digital circuits.
The most common substrate materials used in HDI PCB stackups are FR-4 and Rogers RO4003C. FR-4 is a glass-reinforced epoxy laminate with a dielectric constant of 4.0. Rogers RO4003C is a ceramic-filled PTFE laminate with a dielectric constant of 3.0.
When choosing a substrate material for an HDI PCB stackup, the following factors must be considered:
- The dielectric constant of the substrate material
- Thermal conductivity of the substrate material
- Coefficient of thermal expansion (CTE) of the substrate material
- Mechanical strength of the substrate material
Dielectric Constant
The dielectric constant of the substrate material is an essential factor in determining the signal integrity of high-speed digital circuits. The substrate material’s dielectric constant affects the signals’ propagation velocity and impedance of the transmission lines. A higher dielectric constant results in a lower propagation velocity and a higher impedance.
Thermal Conductivity
The thermal conductivity determines the heat dissipation from the high-speed digital circuits. The substrate material’s thermal conductivity alters the heat’s ability to dissipate from the circuit to the surrounding environment. More thermal conductivity leads to better heat dissipation.
Coefficient of Thermal Expansion
The coefficient of thermal expansion (CTE) of the substrate material is another critical factor in determining the reliability of the HDI PCB. The CTE of the substrate material varies the dimensional stability of the HDI PCB stackup. A higher CTE means that the substrate is in a more significant expansion and contraction of the HDI PCB stackup with temperature changes.
Mechanical Strength
The mechanical strength of the substrate material is an important factor to consider in HDI PCB stackups. The substrate must be strong enough to support the weight of the components and the trace widths. The substrate must also be stiff enough to prevent warping and bending under thermal and mechanical stress.
Dielectric Layer
As the name suggests, a dielectric layer is an insulating material sandwiched between two conductive layers in an electronic device. The dielectric layer of an HDI PCB stackup plays an essential role in providing electrical insulation between the different layers of the circuit board. It also helps to protect the components from electrical damage. The dielectric layer comprises an insulating material such as glass, plastic, or ceramic. It is usually sandwiched between two conductive layers such as copper or aluminum. The thickness of the dielectric layer can vary from a few microns to several millimeters.
The dielectric layer also affects the speed at which electrons flow through the circuit. The thicker the dielectric layer, the slower the electrons can flow. This is why HDI PCBs have a thinner dielectric layer than traditional PCBs. The thinner dielectric layer allows for faster electron flow and, thus, higher speeds.
Conductive Layer
The conductive layer is responsible for providing electrical connectivity in an HDI PCB. It consists of a thin sheet of metal, typically copper, laminated onto the substrate material. The most common metals used for this purpose are copper and aluminum. However, other metals such as nickel and gold can also be used. The conductive layer can be either solid or perforated. Perforated conductive layers are typically used for multilayer HDI PCBs.
The primary function of the conductive layer is to provide an electrical connection between the components that make up the HDI PCB. The thickness of the conductive layer is typically between 0.5 and 2 mils (thousandths of an inch). The most common thicknesses used are 1, 1.5, and 2 mils. The width of the conductive traces is typically between 8 and 10 mils.
Solder Mask
The solder mask or solder resists is a thin layer of lacquer-like material that covers the exposed copper surfaces of a printed circuit board (PCB) and protects them from oxidation and solder bridging. The primary function of the solder mask is to prevent short circuits between adjacent conductors (pads) and to provide mechanical protection to the exposed copper circuitry.
The solder mask is typically applied to both the front and back sides of a PCB and is usually the last material to be added in the PCB fabrication process. Depending on the application, the solder mask can be applied before or after the component mounting process.
The thickness of the solder mask layer is typically in the range of 8-12 microns (0.008-0.012mm). The solder mask material is generally applied using a screen printing process, and the thickness of the final layer is controlled by the mesh size of the screen used in the printing process.
Manufacturing Process
HDI PCBs are manufactured using microvia drilling, in which tiny holes are drilled through the substrate and dielectric layer to connect the conductive layers. This process allows for precise placement of the circuitry, which is essential for HDI PCBs.
Advantages of HDT PCBs
HDI PCBs offer several advantages over traditional PCBs. They are much lighter and thinner, making them ideal for portable electronic devices. They also have a higher interconnect density, allowing for more circuitry to be placed on a given HDI PCB.
Due to their increased manufacturing complexity, HDI PCBs are also more expensive than traditional PCBs. However, the benefits of HDI technology are often seen as worth the extra cost.
Final Thoughts
If you are considering using HDI PCB or Flex pcb in your next electronics project, consult with a qualified manufacturer to ensure that your project is designed and manufactured correctly. Hemeixin HDI PCBs are an excellent choice for many modern electronic devices, and their use will only likely increase in the future.