If your business’s measurements are inaccurate, you risk wasting time and materials making products that don’t meet your customers’ specifications. You also increase the chances of accidents and equipment malfunctions if you’re working with dangerous machinery such as an oil rig’s suction line. Here are a few ways to increase your business’s measurement accuracy, which lets you save time and money.
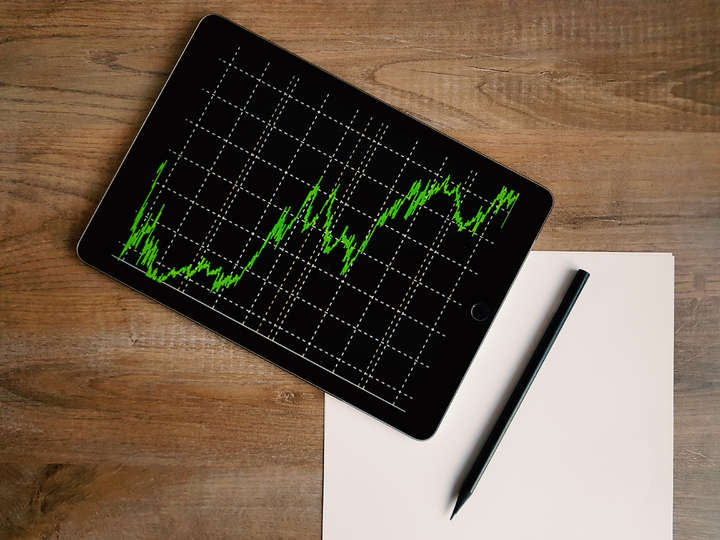
Use a Transducer From Hammer Union
Every machine has an acceptable level of pressure, and if it surpasses this threshold, it overheats or shuts down. When your equipment is operating under intense pressure, it cannot deliver accurate measurements or complete its required tasks. Use a Hammer Union pressure transducer to monitor your pressurized equipment’s levels without taking a manual reading. This tool fits with various machines, including mud pumps, cement trunks, and choke manifolds.
Rely on Automated Equipment
As much as possible, use automated equipment from Hammer Union and similar manufacturers for all your measurements. Even if you have top-notch math skills and new measuring tools, automated measuring tools can perform the same calculations much more quickly and accurately, giving you more time to work on complex problems such as personnel issues.
You can find automated measuring equipment for almost every application:
- Measuring distances
- Calculating slopes
- Maintaining pressure
- Determining volume
The more you incorporate automated equipment into your business model, the more accurate your measurements are and the more efficiently you can work.
Perform Calibrations Regularly
Automated measuring tools need to be calibrated regularly to maintain their accuracy. How frequently your equipment needs to be calibrated depends on which company made it, how often you use it, and how well you maintain it. For example, many pressure transducers only need to be calibrated once per year. However, if your equipment regularly operates at the highest recommended pressure or you drop your transducer a lot, it probably needs to be calibrated sooner.
If your equipment stops giving you reliable results, it’s time to calibrate it. Read your user’s manual carefully because while some manufacturers have calibration guides, others require you to send the equipment back to them. The basic process involves setting up a control measurement with manual equipment or a properly calibrated automated tool and then adjusting your equipment’s measuring mechanism until it delivers the same measurement. Check your manual or industry guidelines to determine the acceptable margin of error.
Choose the Right Tools
Some measuring equipment seems very similar, but you may not get what you need if you don’t look carefully at what you’re buying. For example, transmitters and transducers have similar functions, but transmitters use milliamps for delivering their signals, and transducers use volts. If you don’t have the right equipment, you could misread the measurement and give your employees or clients the wrong information.
Similarly, when you’re choosing tools, you also must ensure that they are rated for the kind of work you’re doing, or else they won’t perform well or last. For example, if you’re working on an oil rig, you need measuring equipment that can handle intense vibration, or it may deliver incorrect measurements.
Take Care of Your Equipment
Your measuring equipment is durable, but you must treat it carefully if you want to keep its readings accurate. Whenever a measuring tool isn’t being used, clean it according to its manufacturer’s instructions. Always put measuring equipment into its carrying case before transporting it to a different site or warehouse. Ensure you know how to turn it on and off properly and keep any safety mechanisms in mind.
Follow these steps to increase your business’s measurement accuracy and deliver better products.